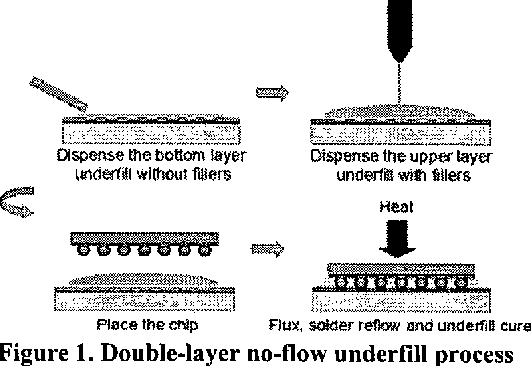
Figure 1 From Novel Filled No Flow Underfill Materials And Process In a novel invention, a double layer no flow underfill is implemented to the flip chip process and allows fillers to be incorporated into the no flow underfill. the effects of bottom layer underfill thickness, bottom layer underfill viscosity, and reflow profile on the solder wetting properties are investigated in a design of experiment (doe. This paper described a wafer level compressive flow underfill process and its involved materials for a novel smt transparent flip chip technology. in this flip chip technology, a liquid fluxable … expand.
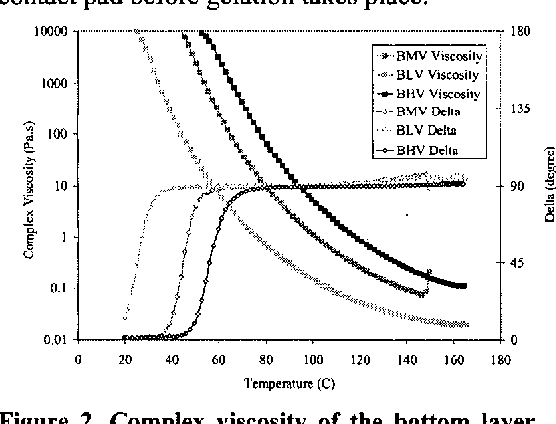
Figure 1 From Novel Filled No Flow Underfill Materials And Process Fig. 1. double layer no flow underfill process. in this paper, the fundamental aspects for processability of the double layer no flow underfill are studied. the important materials and process parameters affecting the yield of flip chip interconnection with filled no flow underfill are investigated. ii. experimental a. materials. To eliminate underfill voiding and the premature failure of components due to solder extrusion into voids, a new no flow processing technique is proposed and developed and shown in figure 1. the process in figure 1 has been demonstrated to produce high yielding, near void free flip chip assemblies (2). The goal of the project was to develop a csp no flow underfill process and compare the reliability of that process to a standard csp process and a standard csp process utilizing conventional underfill. test vehicles were assembled using only solder paste, only dip flux, a fast flow underfill with solder paste, a fast flow underfill. To eliminate voiding and premature component failure due to solder extrusion into voids, a new no flow technique has been developed (figure 1). the new process combines the advantages of conventional capillary flow underfill and conventional no flow underfill processes. the capillary flow dynamic allows for nearly void free assembly.
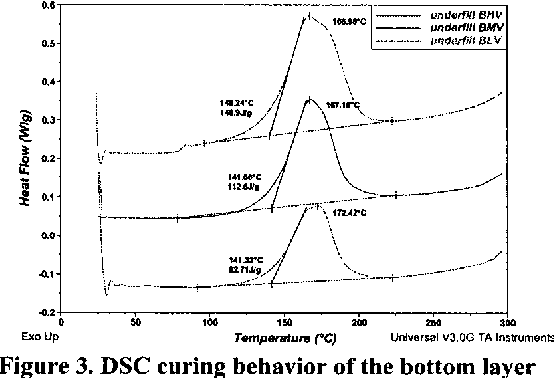
Figure 1 From Novel Filled No Flow Underfill Materials And Process The goal of the project was to develop a csp no flow underfill process and compare the reliability of that process to a standard csp process and a standard csp process utilizing conventional underfill. test vehicles were assembled using only solder paste, only dip flux, a fast flow underfill with solder paste, a fast flow underfill. To eliminate voiding and premature component failure due to solder extrusion into voids, a new no flow technique has been developed (figure 1). the new process combines the advantages of conventional capillary flow underfill and conventional no flow underfill processes. the capillary flow dynamic allows for nearly void free assembly. Abstract— most no flow underfill materials are based on epoxy anhydride chemistry. due to the sensitizing nature, the use of anhydride is limited and there is a need for a no flow underfill using nonanhydride curing system. this paper presents the development of novel no flow underfill materials based on epoxy phenolic resin system. This paper reviews the recent advances in the material design, process development, and reliability issues of flip chip underfill, especially in no flow underfill, molded underfill,. No flow underfill technology has been proven to have potential advantages over the conventional underfill technology. however, due to the filler entrapment between solder bump and contact pad on board, no flow underfills are mostly unfilled or filled with very low filler loading. With the advance of lead free interconnection due to the environmental concerns, a new no flow underfill chemistry needs to be developed for lead free solder bumped flip chip applications. many epoxy resin hexahydro 4 methyl phthalic anhydride (hmpa) metal acetylacetonate material systems have been screened in terms of their curing behavior.
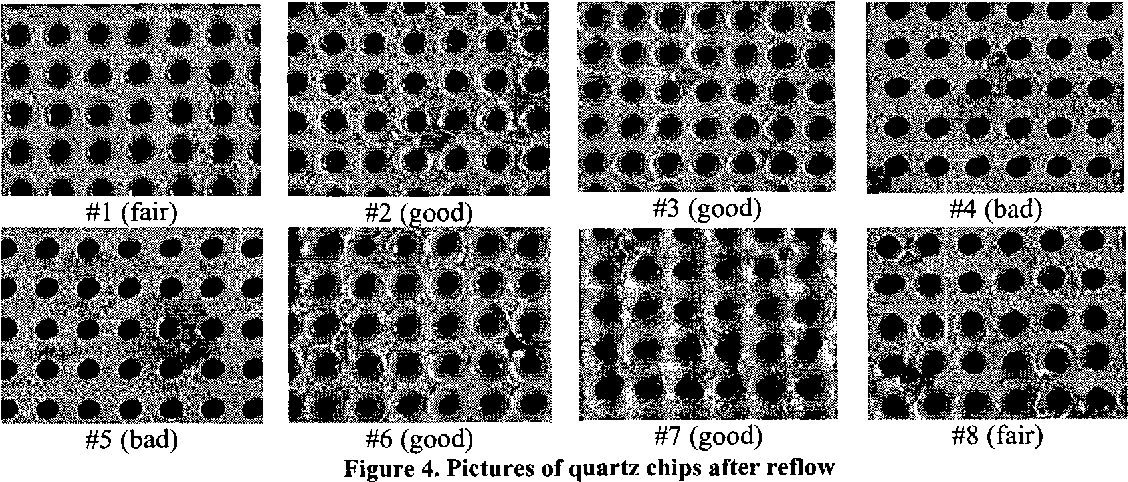
Figure 1 From Novel Filled No Flow Underfill Materials And Process Abstract— most no flow underfill materials are based on epoxy anhydride chemistry. due to the sensitizing nature, the use of anhydride is limited and there is a need for a no flow underfill using nonanhydride curing system. this paper presents the development of novel no flow underfill materials based on epoxy phenolic resin system. This paper reviews the recent advances in the material design, process development, and reliability issues of flip chip underfill, especially in no flow underfill, molded underfill,. No flow underfill technology has been proven to have potential advantages over the conventional underfill technology. however, due to the filler entrapment between solder bump and contact pad on board, no flow underfills are mostly unfilled or filled with very low filler loading. With the advance of lead free interconnection due to the environmental concerns, a new no flow underfill chemistry needs to be developed for lead free solder bumped flip chip applications. many epoxy resin hexahydro 4 methyl phthalic anhydride (hmpa) metal acetylacetonate material systems have been screened in terms of their curing behavior.
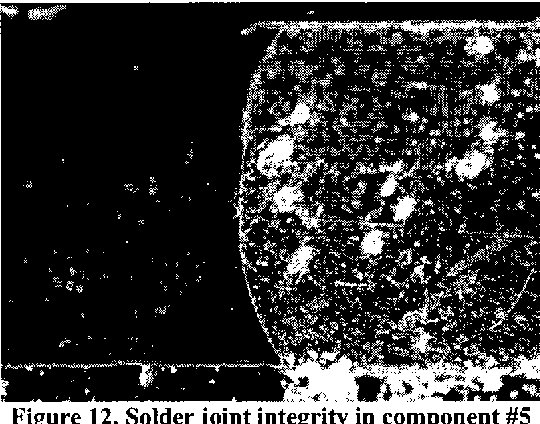
Figure 1 From Novel Filled No Flow Underfill Materials And Process No flow underfill technology has been proven to have potential advantages over the conventional underfill technology. however, due to the filler entrapment between solder bump and contact pad on board, no flow underfills are mostly unfilled or filled with very low filler loading. With the advance of lead free interconnection due to the environmental concerns, a new no flow underfill chemistry needs to be developed for lead free solder bumped flip chip applications. many epoxy resin hexahydro 4 methyl phthalic anhydride (hmpa) metal acetylacetonate material systems have been screened in terms of their curing behavior.
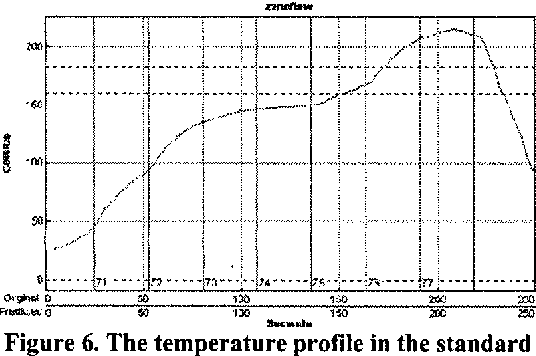
Figure 1 From Novel Filled No Flow Underfill Materials And Process