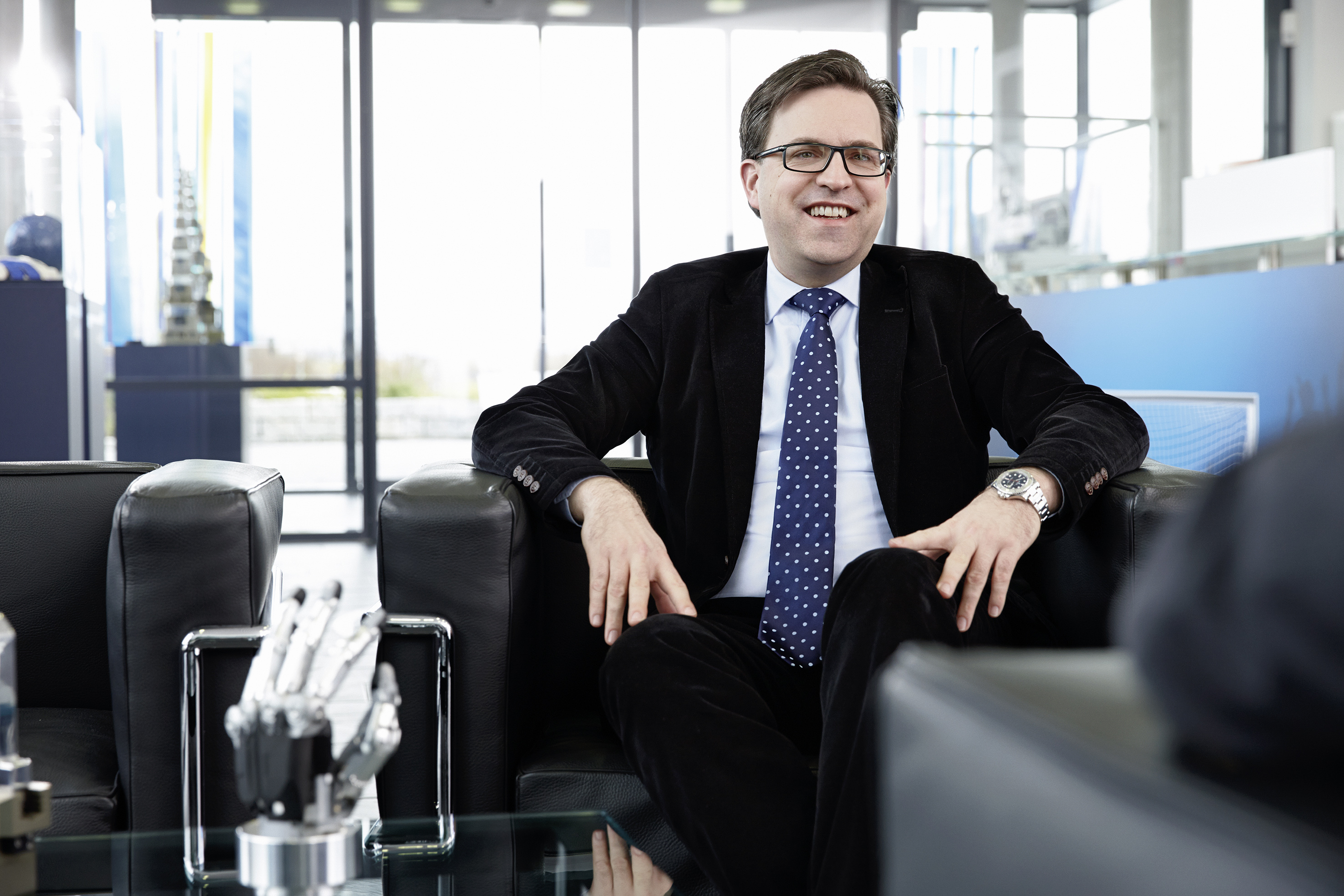
Smart Clamping And Gripping Machine Insider A global first: the automatically adjustable run out and conical run out compensation based on hydraulic expansion technology is enabling a leap forward in terms of quality for high precision workpiece clamping with tolerances of just a few micrometers. Toolholder manufacturers have responded with a variety of rigid, highly secure systems offering anti pullout protection. these include shrink fit, hydraulic expansion and locking toolholders. each features high gripping torque (clamping force) for a tight friction fit on the tool shank.
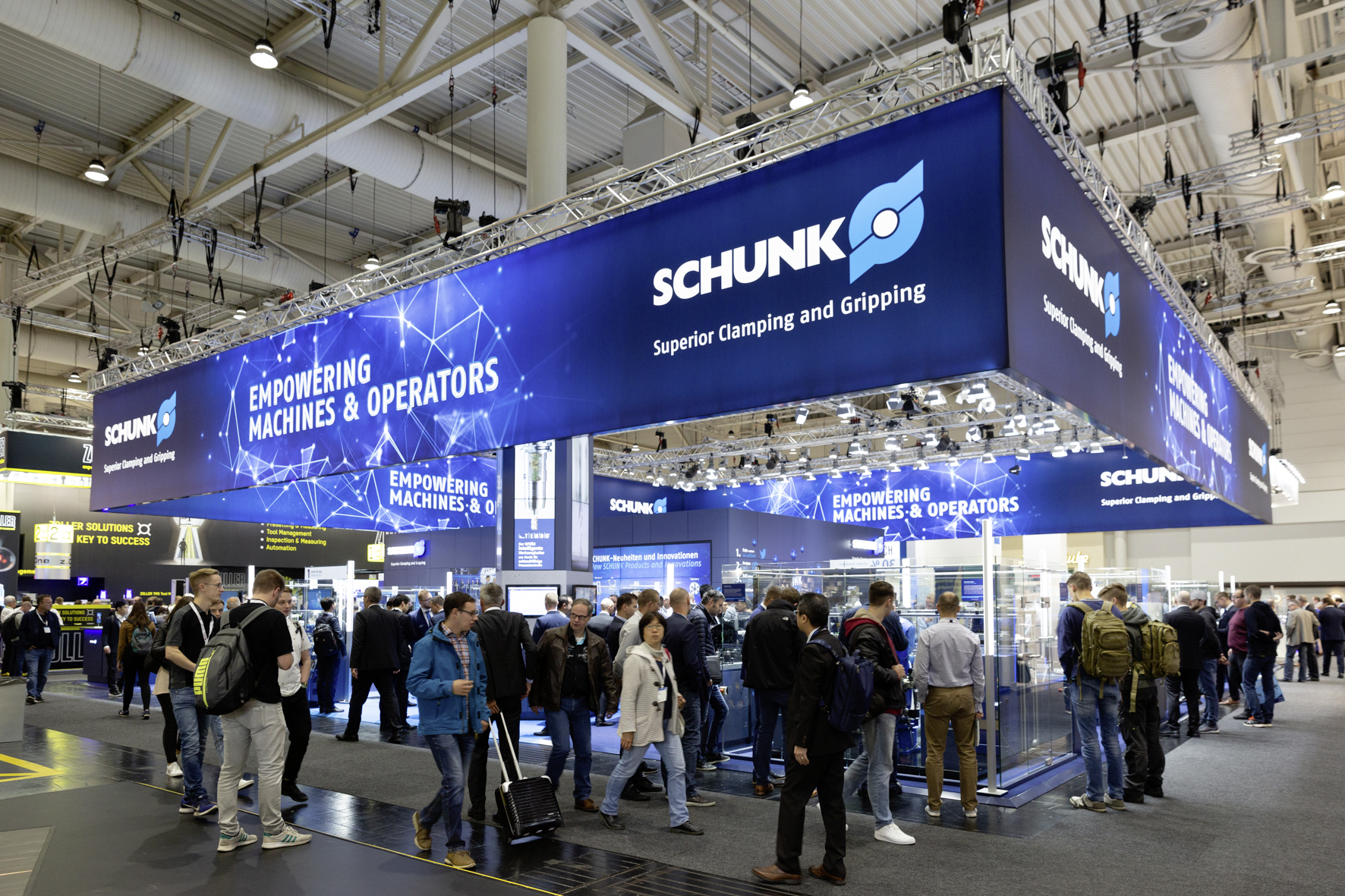
Smart Clamping And Gripping Machine Insider Schunk is going one step further with “smart gripping”, best illustrated by a high speed depanelling system from its subsidiary schunk electronic solutions. From now on, clamping is smart: röhm, the clamping and gripping specialist based in sontheim an der brenz (baden württemberg, germany), is presenting its world premiere ijaw at amb in stuttgart. it is the first chuck jaw ever to be equipped with sensor technology and wireless data transmission. Towards that our industries need to upgrade to the latest technologies in automated clamping and work holding systems where amf is not only a pioneer but also a leader. Great for all turning machine owners: they can now retrofit röhm's ijaw smart clamping jaw without having to integrate the technology into the machine's control system. this means that existing turning machines can be easily upgraded to the smart clamping jaw era.
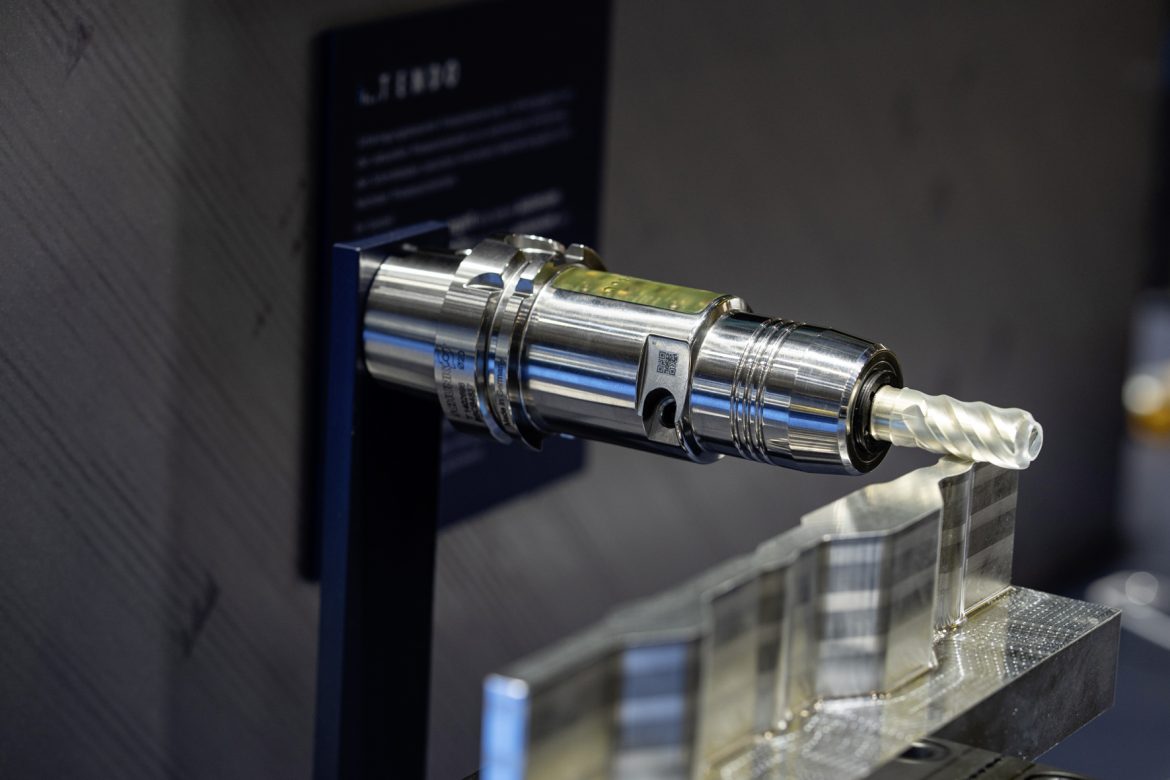
Smart Clamping And Gripping Machine Insider Towards that our industries need to upgrade to the latest technologies in automated clamping and work holding systems where amf is not only a pioneer but also a leader. Great for all turning machine owners: they can now retrofit röhm's ijaw smart clamping jaw without having to integrate the technology into the machine's control system. this means that existing turning machines can be easily upgraded to the smart clamping jaw era. The smart itendo from schunk enables real time process monitoring and control directly on the tool. the geometry and performance data of the toolholders remain unchanged no matter if it is equipped with a sensor system or not. For the first time, schunk presents a sensory quick change pallet module in the field of vero s quick change pallet technology that allows permanent monitoring of the pull down force, the clamping slide position, workpiece or pallet presence. Dmg mori has found a suitable answer with the e pallet, a smart interface for controlling electrical and hydraulic devices. the e pallet interface can provide power for all electric clamping devices with 48 v and 50 a via docking. Smart and automated vertical toggle clamps are changing the way industries work, improving efficiency, precision, and safety. in this blog, we’ll explore how these advanced clamps are shaping the future of manufacturing and whether they’re worth considering for your workshop or production line.