Ipc Plating Specifications Pdf Printed Circuit Board Standard The ipc 6021b standard has included a copper wrap plating requirement for via in pad structures. the filled copper plating should continue around the edge of the via hole and extend onto the annular ring surrounding the via pad. Ipc technical question of the week: what are ipc's requirements for copper wrap plating in through hole vias?.
Everything You Need To Know About Copper Wrap Plating Pdf Ipc 6012b specifies that copper wrap plating shall be continuous from the filled plated hole onto the external surface of the plated structure and extend by a minimum of 25 microns (984 micro inches) where an annular ring is required. figure 1 shows this requirement. This paper discussesa through hole copper filling process for application to high density interconnects constructions and ic substrates. the process consists two acid copper plating cycles. Ipc tc 500 specification for copper plated through hole, two sidedboards,rigid. 3.0 testspecimen 3.1 description of specimens. the following types of specimens can be tested using the equipment specified herein: (1) printed wiring boards, either two sided or multilayer, whichcanfitproperlywithintheneckofthetestmeter. What is copper wrap? 4 figures and text are adapted from ipc t 50. the electrolytic hole plating, extending onto the surface from a plated via structure. in certain pcb fabrication processes a planarization process reduces the wrap thickness.
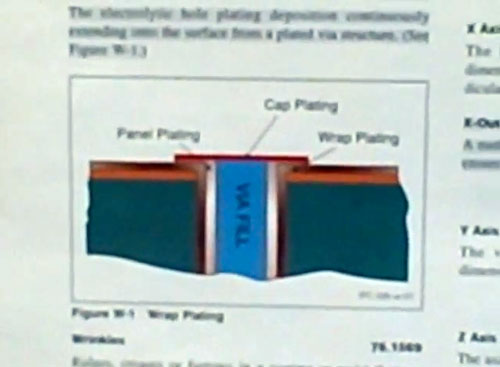
What Are Ipc S Requirements For Copper Wrap Plating In Through Hole Ipc tc 500 specification for copper plated through hole, two sidedboards,rigid. 3.0 testspecimen 3.1 description of specimens. the following types of specimens can be tested using the equipment specified herein: (1) printed wiring boards, either two sided or multilayer, whichcanfitproperlywithintheneckofthetestmeter. What is copper wrap? 4 figures and text are adapted from ipc t 50. the electrolytic hole plating, extending onto the surface from a plated via structure. in certain pcb fabrication processes a planarization process reduces the wrap thickness. In terms of wrap plating requirements for via in pad structures, ipc 6012b states that wrap plating is required for all vias that are in contact with a surface mount pad or hole pad. the wrap plating should extend a minimum of 0.025mm (1mil) up the sidewall of the hole or via, and it should provide a continuous electrical connection between the. The ipc specification for class 2 requires a minimum of 0.000197 inch continuous copper wrap from hole wall onto the external surface of a plated structure, and ipc class 3 requires a minimum of 0.000472 inch continuous copper wrap. In ipc standard revisions such as ipc 6012b and 6012e, the requirements of copper wrap plating and wrap plating thickness are specified for all filled plated through holes. the standard classifies electronics designs as class 1 for general electronic products, class 2 for dedicated service electronic products, and class 3 for high reliability. Ipc has released new plating requirements to allow for finer line widths. table 3 10 now requires only 5µm [197 µin] minimum wrap plating for buried vias > 2 layers, through holes, and blind vias. prior to this revision, the minimum wrap plating requirement was 12 µm [472 µin].

Copper Wrap Is The Electrolytic Hole Plating Deposition Continuously In terms of wrap plating requirements for via in pad structures, ipc 6012b states that wrap plating is required for all vias that are in contact with a surface mount pad or hole pad. the wrap plating should extend a minimum of 0.025mm (1mil) up the sidewall of the hole or via, and it should provide a continuous electrical connection between the. The ipc specification for class 2 requires a minimum of 0.000197 inch continuous copper wrap from hole wall onto the external surface of a plated structure, and ipc class 3 requires a minimum of 0.000472 inch continuous copper wrap. In ipc standard revisions such as ipc 6012b and 6012e, the requirements of copper wrap plating and wrap plating thickness are specified for all filled plated through holes. the standard classifies electronics designs as class 1 for general electronic products, class 2 for dedicated service electronic products, and class 3 for high reliability. Ipc has released new plating requirements to allow for finer line widths. table 3 10 now requires only 5µm [197 µin] minimum wrap plating for buried vias > 2 layers, through holes, and blind vias. prior to this revision, the minimum wrap plating requirement was 12 µm [472 µin].